After writing a letter to our mechanic Mr. Diksan I can see that there
is useful information in it for the Morris Minor Owner and other mechanics
and therefore we bring it here without editing.
Best regards
Anton
14.7.2010.
Dear Diksan,
Some time back you reconditioned a 10MA engine for me (1098cc) and
sent it to me. I was not quite happy with the finish and had my doubts
about other things. Also I wanted to check up on the job done in Matara,
boring the cylinders and grinding the crankshaft.
Therefore I took the engine totally apart and inspected every part of
it.
Let me first tell you that you have done a good job and that the engine
would have performed nicely to Sri Lankan standards. But we must do
better and I will tell you about my findings so you can learn something.
Whether the engine will do a few thousand kilometres or a hundred thousand
kilometres without trouble depend on many details. Often it is the small
details that make a difference.
I understand very well your problems with proper spare parts, but there
might be something in the following I have not yet told you.
Cleanliness during any job on a car is essential. This is my work bench
and it is clean before I start taking the engine apart.
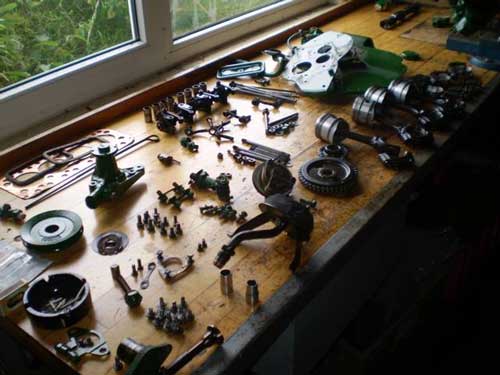
This is my washing basin. It is placed on top of a 200 litre drum with
a special cleaning liquid. At rear in the middle is a 3-way crane. When
I turn the crane to the right compressed air will enter the drum and
press cleaning liquid to the hose with the brush and I can clean and
wash the parts.
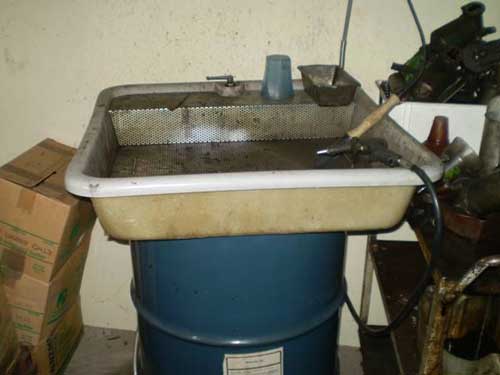
Years back I told you to make something similar. Your cleaning is bad
and now you must complete your washing table immediately. I have also
told Ravindra this and he knows what to do. If in doubt you must ask
me.
As far as I can see you have only run the engine a few minutes, but
the engine oil is black and dirty and I could feel that dust and sand
were inside the engine.
When an engine is newly reconditioned, the engine oil should stay clean
and clear for a while. When shifted in time it should stay clear for
a long time.
Cleaning the engine inside is essential. The bigger problem with this
is cleaning the oil gallery. You can clean the oil gallery with a special
brush. I will bring one next time and show you how.
With your washing table fitted with a pump and brush with a hose and
a few instructions you will be able to do the washing and cleaning properly.
Kerosene is good for washing and cleaning. Do not use petrol.
Painting the engine also add to the quality, especially the finish.
I am brush painting everything, but you can have the oil sump, valve
cover, timing cover, side covers, oil filter housing and the crankshaft
pulley spray painted. The rest you have to brush paint.
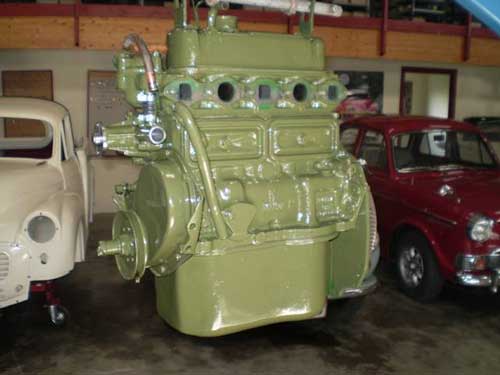
You must not paint inside the engine and where parts are joined. When
you are brush painting it is easy to remove the little that comes in
places where it should not be. You must not paint the back plate, only
the front side when the engine is assembled.
Now I have a big job cleaning the back plate where the gearbox engages.
It would be easy just to remove the little I have put on. The green
colour you are using is not correct but this is not so important. Worse
is that you have painted the flange on the crankshaft where the flywheel
is fitted. This place must be absolutely clean and also all places for
a gasket.
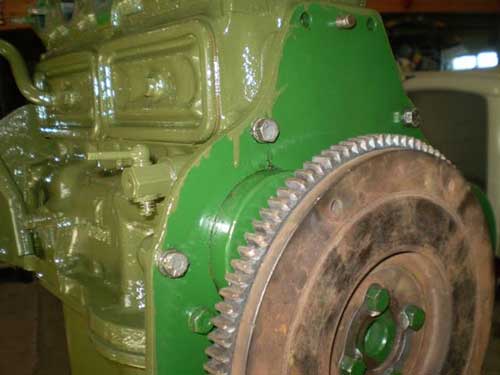
When you are fitting the back plate you have to use some extra bolts
which are only there when the gearbox is fitted.
Gaskets are bedding in after nuts and bolts are tightened and you have
to tighten nuts and bolts one or two times until the gaskets are fully
settled.
When you are fitting the engine sump, back plate, front plate, timing
cover and side covers you have to leave them to rest for a few hours
or until next day if practical and then tighten the nuts and bolts again.
You will easily feel that you can turn the nut or bolt a little, especially
where cork gaskets are used. Careful tightening will prevent many oil
leaks.
In the crankshaft there is a bush, 10M131, for the axle shaft from
the gearbox. If you are in doubt you have to fit a new. You can use
a shaft from a gearbox for fitting. This shaft is also useful when centring
the driven clutch plate. You have to fit a small washer on the shaft
for protecting the bush. The shaft is rounded and if the bush is a tight
fit you can spoil the bush when pressing it in.
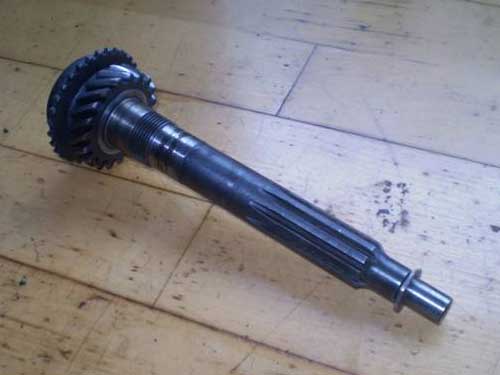
I have told you about the special tools I am using and it was in my
mind to show you all of it when you visit me here in Denmark. Hopefully
you will soon have the visa, but now you have had your own workshop
and we can not wait and we must get started on finding the tools you
are still missing. You are a fast worker and with the right tools you
can save a lot of working hours on a job.
It is important to give the customer good value for his money and already
now I can see that you are doing better than your colleagues in Sri
Lanka. You may think you are fully trained now, but surely you can still
learn a lot.
Actually I am happy now that our old mechanic refused to join us when
we moved from Bataduwa. He was very experienced, but refused to follow
my instructions. You had no experience or bad habits when you joined
and it has been possible for me to teach you something over the years.
We will accelerate teaching you and you will teach your assistants at
your best and in a short time we will be able to do top class jobs only
limited by lack of the right parts.
For the time being you can do better than most mechanics but have to
accept that the customer want it cheap. We will discuss this and agree
on a minimum level of quality. Should a customer not accept our level,
he has to find some other mechanic willing to compromise. Cheap solutions
are always expensive long term and gives a lot of trouble and discussion
with the customer later on.
I have not seen the special spanner for the crank shaft pulley nut
with you? The correct size is not available, but you may find a 32 mm
spanner and machine it to 33 mm as I did. With a good blow from a heavy
hammer it takes no time to remove the nut. Without this spanner it can
take much time and may be you will spoil the nut. On this engine a chisel
and hammer has been used for the job. It was the same with the nut on
the cam shaft, but I know that you have the right socket for this nut.
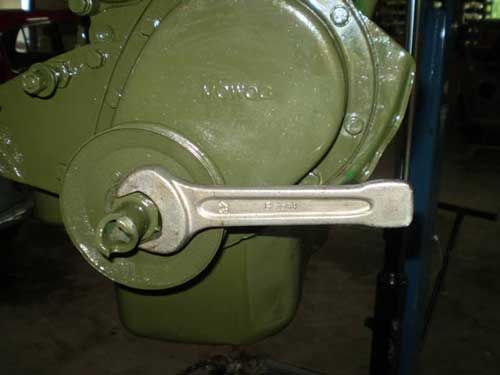
When you work on this nut, the flywheel bolts and the camshaft nut
the crankshaft will turn making the job difficult. You can make a simple
tool yourself for locking the crankshaft from a bracket on the engine
block for the dynamo. Make one now, keep it with your special tools
and make your work safer and much faster.
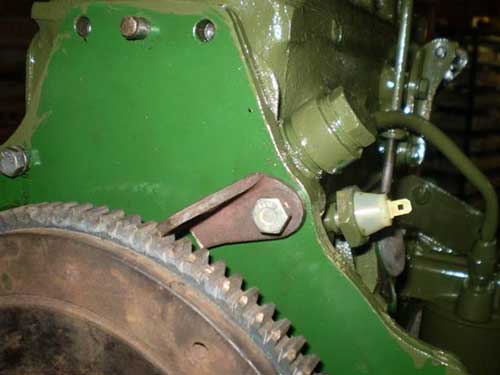
Some of the bolts for the connecting rod bearings were incorrect and
you have had trouble tightening them correctly (35 lb.ft. - 4.8 kg.m.).
It was difficult for me to remove these bolts as the head was rounded.
New bolts are now fitted.
It was exciting to see the way the you have repaired the rear main
bearing cap and the similar part bolted to the engine block. Is this
done by the people in Matara? They have done a very good job grinding
the crankshaft and fitting new cylinder liners. Torque wrench setting
for the main bearing set screws 60 lb.ft. – 8.3 kg.m. Fly wheel set
screws 35-40 lb.ft. – 4.8-5.5 kg.m. Cylinder head stud nuts 40 lb.ft.
– 5.5 kg.m.
I was not so fond of the bearing shells but as we need experience about
quality of parts available locally we will test them and I will ask
my customers to report frequently. Normally the bearing shells are silver
but these were black. Were they silver when you fitted them?
The pistons looked ok but had an extra oil ring. This ring is locked
from rotating. I have never seen this locking of a ring in a Morris
Minor engine and only some 948cc engines have this extra oil ring.
Under the nuts for the cylinder head, rocker shaft and manifold only
flat washers. No spring washers.
The nice cast iron crankshaft pulley is not so good and I have replaced
it. There are no timing mark and no grove for the lock washer.
The oil filler cap is not for a Morris Minor. The rocker cover has been
over tightened and a better one with the correct oil filler plug fitted.
The engine sump has been repaired and the drain plug pointed upwards
and oil could not drain fully. A better one is fitted.
The oil filter housing has been repaired and is now replaced by the
correct housing and lower sealing.
I have replaced the timing wheel cover as it was incorrect and fitted
with a felt oil seal. I have replaced the water pump. It was easy to
feel that the bearings are worn out and although it is not leaking and
would do the job for a while you should not fit a bad water pump. This
pump would fail after a short time and the customer would put the blame
on you.
When removing the oil pipe from the oil release valve to the filter
housing take the big banjo bolt first. Then you will avoid twisting
the pipe near the oil filter housing.
The camshaft locating plate is replaced by a new. It is not good enough
to turn it as the tolerance of camshaft movement will then be too much
and in some cases give a strange sound from the engine.
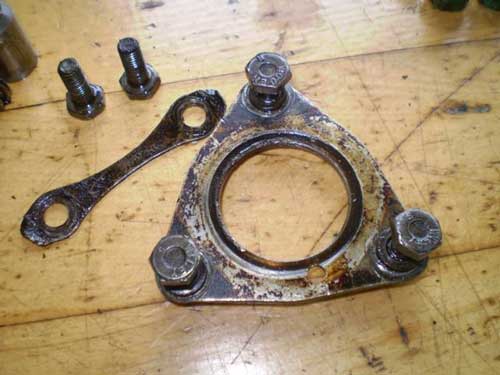
The tube for the oil dipper rod was broken. I pushed out the part of
it still in the engine block and fitted a new one (10M255). Later I
was puzzled by the length of the rod and checked it and found out that
the stopping ring on the rod has been moved about one inch down. May
be to compensate for the broken tube? I replaced the oil dipper rod.
The old one would give a false reading and show too little oil even
it was full.
It has been an entertaining and exciting exercise for me to do this
job and I can see that you are fully qualified for the job. Your only
problem is the right parts and we have to discuss this with Ravindra
and find out what we can do.
Taking the engine apart, cleaning and washing, inspecting, comparing
parts, looking up specifications, putting the engine together and painting
took me about 15 working hours. Usually it takes more time but this
engine was not that dirty. This is only possible because I have everything
needed in house. It will take a long time before you can do this job
in 15 hours as you have to shop around a lot to find what you need.
10 hours more and the engine is fitted into the test bench or a car
and running. How many working hours have you spent on the job?
It will be interesting to see how fast we can improve your facilities
and cut down your hours on a job. I am afraid that it will take many
years before you can do the job in this time. Already now you can do
a job faster and better than many mechanics in Sri Lanka and in a short
time nobody can beat your time and quality. I am looking forward to
discuss this with you next time I am in Sri Lanka.
Best regards
Anton